REVIEWED P2 OPTIONS
| ||
Reviewed Chemical - Agriculture OptionsFollowing are a list of options that have been reviewed by pollution prevention specialists. These options have worked at other facilities and may work at yours. |
||
Use plastic or foam pigs | ||
Use plastic or foam pigs to clean products from transfer lines before equipment is rinsed. This method will reduce the amount of cleaning water needed, but will produce an additional waste stream requiring disposal. | ||
Use specific systems for spills and area washdowns | ||
| ||
Steam clean viscous products | ||
Steam clean viscous products to eliminate wastewater generation and the need for detergent or other cleaning agents (can use steam from on-site boilers or purchase steam cleaning equipment) (Do not steam clean if volatile organic solvents or solvent inerts are present in the product because steam increases the rate of volatilization of organic compounds) | ||
Use drums with liners | ||
Use drums with liners as opposed to plastic drums or bags | ||
Reducing Air Emissions from Fixed Roof Storage Tan | ||
Methods for Reducing Air Emissions from Fixed Roof Storage Tanks:
| ||
Segregate Waste Dusts and Particulates | ||
Segregation will allow recycling of pesticide dust resulting in disposal and raw material costs. | ||
Use Wet Scrubbers | ||
Use a wet scrubber to reduce air emissions | ||
Use Spinning Buckets | ||
Use spinning buckets and implement vibration of spray plates to decrease microprill formation and fine dust loading and emissions. | ||
Vacuum or Sweep Leaks | ||
Sweep or vacuum dry product spills to avoid generating a wastewater stream | ||
Collect liquid spills in a sump or trench | ||
Collect liquid spills in a sump or trench to reuse, dispose, or discharge with a squeegee, mopping up the spill remains. | ||
Collect liquid spills with an absorbent material | ||
Collect liquid spills with an absorbent like absorbent pads or soda ash (can neutralize an acidic product spill) before mopping or spraying to reduce wastewater stream. These absorbents may then require disposal. | ||
Reuse Leaked or Spilled Products | ||
Reuse Leaked or Spilled Products when Possible Use drip pans or other containers used for catching leaks and spills (water or solvent based) for direct reuse into product being processed, formulated, packaged, or stored for a future batch. | ||
Install collection hoppers or rubs | ||
Install beneath packaging fillers catch and redirect spills into fillers | ||
Bring operations indoors | ||
Bring operations indoors or build roofs covering outdoor storage tanks and dikes Roofs kept in good repair and designed to protect crosswinds from mixing rainwater with contaminates will reduce contaminated precipitation runoff. | ||
Install a sump | ||
Install a sump on a transfer or containment pad If operations are outdoors, install a containment or transfer pad (asphalt or concrete with crack sealer and top coat sealer) with a sump to collect rinse water. | ||
Use Low Heat Removal of Carbon Dioxide | ||
Low heat removal of carbon dioxide requires less external heat because flashing is used for part of the regeneration process than traditional systems used to remove carbon dioxide from process steam | ||
Use Process Computer | ||
Use to control and monitor important variables such as hydrogen/nitrogen ratio, steam/carbon ratio, synthesis loop purge, methane leakage, converter control, and refrigeration | ||
Install a wastewater evaporator system | ||
Install a wastewater evaporator system to reduce the amount of contaminated cooling water discharge (wastewater) and effectively make use of nitrogen in ammonium nitrate production. | ||
Designate Laboratory Sinks to Specific Products | ||
During laboratory equipment cleaning operations, designate laboratory sinks to specific products and collect wastewater from the testing for reuse in the same product or to transfer back to the AI manufacturer or the product registrant (solvent contaminated water resulting from quality control tests in a laboratory on solvents may not be able to be reused) | ||
Substitute a contained water bath | ||
Substitute a contained water bath for a continuous overflow bath to reduce the volume of water used. | ||
Pave areas where spills occur frequently | ||
Segregate solid waste | ||
Store and reuse cleaning wastes | ||
Control Air Emissions | ||
| ||
Maximize production runs | ||
To reduce Equipment Cleaning Waste | ||
Designate equipment hard to clean formulations | ||
Designate equipment (possibly only mix tank or agitator) for hard to clean formulations | ||
Package products directly | ||
Package products directly from formulation vessels
Use raw materials to package final products | ||
Return containers | ||
Return containers to the supplier | ||
Reuse containers | ||
Reuse as directed | ||
Strict quality control and automation | ||
Off-Specification Products Strict quality control and automation Reformulating off-spec batches | ||
Use low volume cleaning | ||
Use low volume, high efficiency cleaning | ||
Triple rinse | ||
Triple rinse raw material shipping containers with solvent that will be used in the formulation so the rinsate can be directly added to the formulation. (Pesticide chemicals formulating and packaging facilities and pesticide repackaging and refilling facilities should make certain they will still be in compliance with effluent guidelines found in 40 CFR 455 Subparts C and E before implementing this change.) Use a high pressure/low volume rinse out system for triple rinsing. | ||
Utilize Drum Rinsing Stations | ||
Utilize these to reduce wastewater generation during shipping. | ||
Reuse Drum Rinsate | ||
Reuse drum rinsate directly in the formulation when appropriate or treat and reuse for imminent drum and equipment rinsing. | ||
Schedule production to minimize tank cleanouts | ||
Schedule production to reduce instances of product changeovers which can minimize cleanout occurrences. Schedule products in a logical order if they have common active ingredients and the same solvent (or water) base. | ||
Schedule Products According to Packaging | ||
Schedule Products According to Packaging to reduce changeover cleanings of packaging equipment. | ||
Adjust Packaging Line | ||
Minor adjustments to packaging lines may prevent using an additional set of packaging equipment which would constitute additional cleaning. | ||
Perform Packaging Out of Formulation Vessels | ||
Performing packaging directly out of formulation containers to prevent using additional tanks and hoses in addition to cleaning them. | ||
Segregate equipment | ||
Segregate equipment (processing/formulating/packaging)by individual product. | ||
Segregate solvent formulations | ||
Segregate solvent based and water based formulations. Dedicate a line to solvent-based products and a line to water-based products allowing for reuse of water or solvent. | ||
Segregate products | ||
Segregate products containing similar active ingredients in variable concentrations | ||
Use Hand-Controlled Devices with Hoses | ||
Prevents water flow previously generated by unattended hoses | ||
Use wastewater reduction equipment | ||
Equipment that reduces or eliminates wastewater generation:
| ||
Clean up spills and leaks outside in bulk containm | ||
Clean up spills and leaks outside in bulk containment areas in order to avoid contaminating storm water | ||
Place drip pans under valves and fittings that lea | ||
Place drip pans under valves and fittings that leak and under valves and fittings where hoses or lines are habitually connected and disconnected. | ||
Perform preventative maintenance | ||
Perform preventative maintenance on all valves, fittings, and pumps | ||
Dedicate tanks for formulation mixing | ||
This will eliminate one of the most common contaminated wastewater stream |
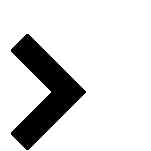