REVIEWED P2 OPTIONS
| ||
Reviewed Cleaning and Degreasing Operations OptionsFollowing are a list of options that have been reviewed by pollution prevention specialists. These options have worked at other facilities and may work at yours. |
||
reduce solvent evaporation | ||
Increase the freeboard height to significantly reduce solvent evaporation. | ||
automatic parts lift | ||
Install automatic parts lift on vapor degreasers | ||
Use drain racks | ||
Use drain racks to reduce dragout. | ||
use rotating rack. | ||
Drain parts using a rotating rack. | ||
Clean parts | ||
Determine whether parts need to be cleaned. | ||
Use rust inhibitors and lubricants | ||
Use easy-to-clean or no-clean rust inhibitors and lubricants | ||
Review handling process | ||
Review the handling process of the parts to determine why parts are getting dirty and take action to prevent it from happening in the future. | ||
clean stock | ||
Purchase clean input clean | ||
Use elbow grease | ||
Use elbow grease. When possible, clean by brushing and wiping. | ||
Use aqueous-based cleaners | ||
Use aqueous-based cleaners | ||
Use Solvents | ||
Use solvents with a low vapor pressure and high flash point. | ||
Use citrus or terpene cleaners. | ||
Use citrus or terpene cleaners. | ||
Keep lids on | ||
Keep lids on your solvent-cleaning vessels. | ||
air-lock vapor degreaser | ||
Use an air-lock vapor degreaser | ||
reduce drafts | ||
Minimize evaporation by reducing drafts. | ||
Install refrigerated coils | ||
Install refrigerated coils on the freeboard above the primary condenser coils. Working emissions are reduced by approximately 20-50 percent for above freezing coils and 30-80 percent for below freezing coils. | ||
Use counter-current rinsing. | ||
Use counter-current rinsing. | ||
reuse aqueous cleaners. | ||
Skim/filter and reuse aqueous cleaners. | ||
install filtration or distillation units. | ||
Reuse solvents by installing filtration or distillation units. | ||
Install bioremediation parts washer | ||
Install a bioremediation parts washer that uses enzymes to eat oil and grease. | ||
Segregate solvents | ||
Segregate solvents to allow recycling | ||
Keep solvents out of used oil. | ||
Keep solvents out of used oil. | ||
Keep fluids out of solvents | ||
Keep fuel, brake fluid, and other fluids out of solvents to prevent the mixture from becoming hazardous. | ||
Keep solvents out of aqueous cleaners. | ||
Keep solvents out of aqueous cleaners. | ||
solvent storage. | ||
Use secondary containment for solvent storage. | ||
fix and prevent leaks. | ||
Implement a maintenance program to fix and prevent leaks. | ||
increase drain time. | ||
Reduce dragout by increasing drain time. | ||
reduce dragout. | ||
When dipping parts, lift them such that it reduces dragout. | ||
Install lids | ||
Install sliding lids on solvent tanks. |
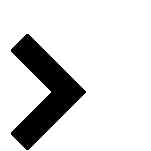